Wire Tying Machines
Streamlines of the furnace brazing process : WOS Wire Tying machines
COMCO WOS Wire Tying machines eliminate the use of brazing jigs for brazed heat exchangers. Process cost reductions include:
- Braze jig cost elimination
- Furnace throughput increase
- Furnace energy reduction
- Improved braze quality
Full Automatic: WOS-A series
- Fully automated wire winding
- Single or multiple simultaneous wire application
- Numerical wire tension and core compression control
Semi Automatic: WOS-S series
- Semi automatic wire tying
- Numerical wire tension and core compression control
Optional Features
- Servomotor controlled core compression
- Load Cell core compression force measurement and display
- Automated wire position-to-position indexing
- Cycle time control of process cycles
- Custom features by request
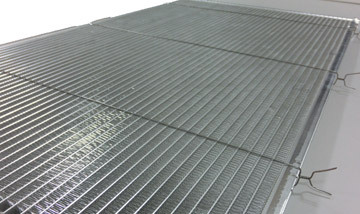
Wire tying position is programable
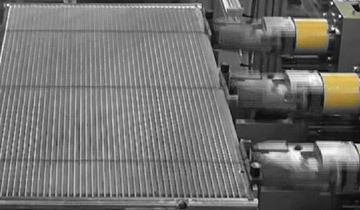
Multiple wire tying head for better output
Benefits of Wire Tying for Brazing
- Wire elastic properties reduce compression buckling of fins during brazing
- Elimination of model specific brazing jigs
- Elimination of brazing jigs storage areas frees plant floor space
- Elimination of brazing jigs maintenance labor and costs
- Reduced furnace energy cost
- Increased furnace throughput
- Increased furnace conveyor belt and muffle life
For more detail, or a consultation, contact a COMCO worldwide regional location or office.
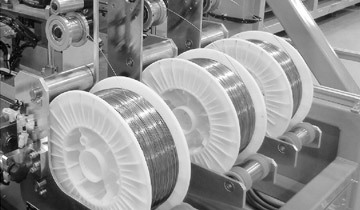
Wire bobbin brake system for stable wire tension control